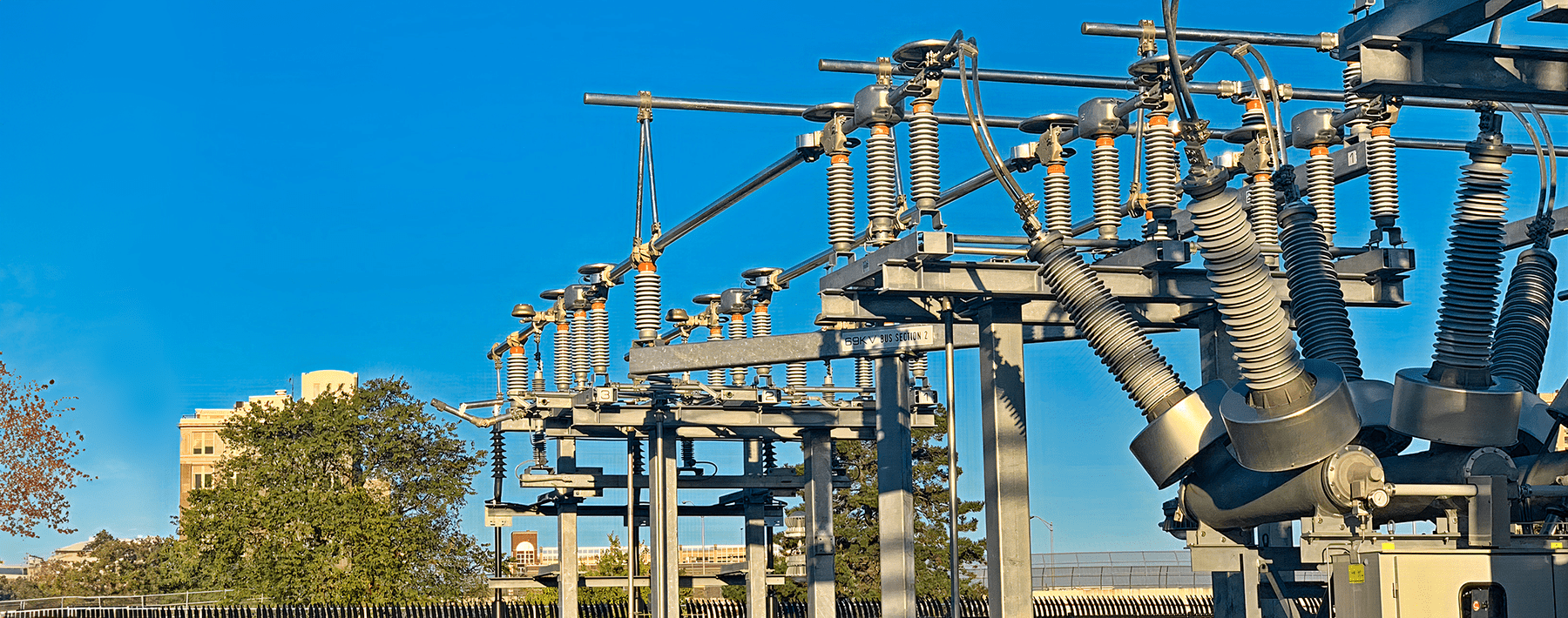
Contamination solutions
Lapp’s Resistance Graded RG® Insulators excel in heavily contaminated areas, significantly reducing operational costs and the risk of flashover. Please see below to learn more.
With the first Lapp RG® insulator installation dating back to the 1970s, no other manufacturer matches our level of experience. RG® insulators are designed to prevent contamination-related flashovers. Each insulator, produced at our LeRoy, NY factory, undergoes rigorous 100% testing and can be traced by individual serial number, ensuring unparalleled reliability and performance.
No other manufacturer comes close to Lapp’s semiconductive glaze experience. Our LeRoy facility has been refining the RG® manufacturing process and rigorously testing this technology for over 50 years with evolving technological improvements.
Lapp’s RG® Resume:
Lapp’s RG® Insulators were designed to eliminate the need for washing and greatly reduce the risk of contamination related flashovers. Even in areas where contaminants form thick deposits on the insulator surface, our RG® technology will prevent dry band arcing and insulator flashover. Common application areas for these products include:
Salt fog and sea salt
Coal plants, power generation facilities, cooling towers
Agricultural contaminants, Machinery exhaust
Heavily traveled areas, roadway salt
The benefits of RG® Insulators are a result of the semi-conducting glaze that is baked onto the porcelain body, becoming an integral and permanent part of the insulator. RG® is available on our station posts, line posts, struts, apparatus porcelain, and long rod insulators.
RG® has more benefits than shown here. For additional information please reference the downloadable materials below or contact your local representative.